Unlike 20 years ago, most of today's blades are able to pitch and this will increase as new techniques are introduced. Hydraulic systems or more complex electrical drives will be required, adding more moving parts and so more failures. Electrical controls have also become much more complex. Today's technicians need to be much more knowledgeable - and what used to be a few days' training from the turbine supplier now extends over a few weeks.
Some companies separate out expertise into mechanical and electrical maintenance. There is also a trend for specialist companies to perform inspections on items such as elevators, cranes and the fire-extinguisher installations used on large offshore turbines. Or maintenance personnel go to the manufacturer for training. Yet still there is a bottleneck in knowledge. I believe that training is one of the most important requirements for improved wind turbine operations and maintenance (O&M).
As a turbine inspector and consultant, I often work out in the field and regularly notice a lack of education to conduct proper O&M jobs, or insufficient knowledge of the background to failures linked to a particular turbine model or the technologies in place. Just looking at the logbook of a turbine can show that the service technicians have to come back more frequently to solve problems that could have been picked up or checked while on site.
Health and safety knowledge for the employees, however, has greatly improved in the last two years, as workers are now required to be trained before they can start work. Learning how to leave the nacelle quickly, by descending on a rope, gives them greater confidence. And I know of a few occasions when the training for rescuing colleagues from inside the wind turbine has already been put into good practice. Happily at smaller injuries, but still ...
One potential for a reduction in upkeep costs may come through direct-drive or medium-speed wind turbines, both of which are being investigated by a number of suppliers. One reason for this is simply that there is a major reduction in the number of parts. Also, around 70% of the gearbox problems that I have observed originate at the high-speed output shaft section.
Assume the turbine rotor turns at 20rpm, in a high-speed geared system the fast-speed shafts and bearings are rotating at 1,500rpm, 24 hours a day, and 350 days a year (the other days are for maintenance and failures). With a direct-drive machine, the generator and rotor turn at the same speed. And with a medium-speed gearbox the speed difference is much smaller - in both cases eliminating many of the potential problems.
Operators of small wind farms can gain much by joining forces with other operators of similar turbine types. In Germany there are many owner groups that together hire post-warranty maintenance companies. Some even stock spare essential components such as gearboxes, bearings and rotor blades so that if there is a failure, stoppage time is as short as possible. I know owner of 12 wind turbines who manages his own spares stock and hires in an independent service provider to ensure optimal availability, achieving substantial cost savings.
Owners of larger wind farms often do something similar and agree during the warranty period to stock some essential components, while some involve their employees during warranty-period services.
Developers are also recommended to team up with a qualified technical adviser and legal advisers during the contracting phase. That way, if failures start to develop, early discussions can begin about whether it is "normal" wear-and-tear or a structural failure that might point towards design issues that could repeat post-warranty.
I had expected that condition monitoring systems (CMS) would significantly affect current maintenance of wind turbines, but what I see now tells me that it is not making a big difference yet. This is largely because of the limited ability to interpret the CMS data accurately. I expect it will be another five or seven years before CMS will properly deliver the accurate and detailed information we need.
Today's maintenance is more professional than ever. Techniques and knowledge are more comprehensive, and working with other owners allows the operators and owners to share information, secure key components, and have some power to represent themselves to suppliers.
Jan van Egmond is managing director of Quality in Wind and a senior wind turbine inspector and technical consultant, with over 20 years' experience in the industry
Modern turbines continue to push technicians' knowledge
As turbines have grown and some elements of repair and care have reduced in relation to power output, the introduction of more complex systems has meant that the job of keeping them running has not reduced proportionately. It may even have increased.
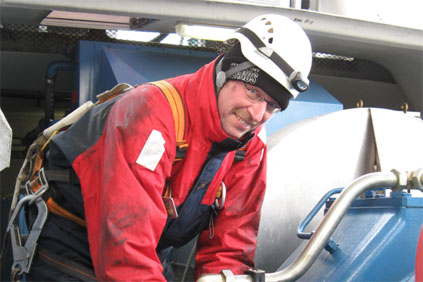