Conventional met masts installed offshore as semi-permanent structures involve costly logistics and permitting. "These are monopile or other seabed mounted support structures with met mast. For both installation and removal operations jack-up vessels are required, plus expensive offshore commissioning. Effective use of the structures is typically one to a few years," explains BMO commercial director, Bart Ummels. "Furthermore, permitting procedures for installing permanent offshore structures have proven cumbersome and time-consuming, while adverse environmental impacts arising during monopile ramming have to be considered, too."
BMO Offshore’s FlexMetMast consists of a floatable tripod with legs extending towards a box-shaped deck structure and a met mast on top. All measuring instruments and two diesel-generator sets for providing power supply are well protected inside this deck box. The met mast will be fitted with wind-speed measuring equipment at different elevations, including hub height. Additional instruments are incorporated to the FlexMetMast structure for conducting wave and scour measurements. A patent is pending on BMO Offshore’s technology.
Fully instrumented, pre-tested and commissioned FlexMetMasts can be towed from sheltered harbours to wind farm construction sites, where the structure is lowered onto the seabed and temporarily secured by, for instance, suction anchors.
The cost savings that this approach offers are significant, argues Ummels. "Banks demand a full year of wind speed measuring for a complete business case." While Ummels declined to offer specifics, he indicated that cost savings of 50% are achieved when FlexMetMast is deployed. He added that savings at this scale are possible at "both average water depths and more costly deep-water sites".
In addition, BMO Offshore’s product can be deployed repeatedly, allowing costs to be spread over time. Once a measuring campaign is completed, the FlexMetMast can be brought back in floating position and towed to the next offshore site. "Sensor equipment and steel structure investment costs can be spread over multiple measuring campaigns," explains Ummels. "Another added benefit is that the concept has been classified as a vessel and thus no permitting is required."
BMO Offshore believes that the commercial strengths of its technology are not threatened by alternative options, such as a vessel-mounted Lidar or a Lidar device replacing a fully instrumented met mast. "Banks do not accept data obtained by Lidar as sufficient proof," claims Ummels, adding that "BMO will install Lidar in parallel to a met mast fitted with conventional anemometers for verification and R&D purposes."
For certified analysis of measurement data and technical support, BMO has partnered with Dutch energy research centre ECN. Two other key project partners are F2F – responsible for the FlexMetMast design and itself a partnership between Ulstein Sea of Solutions and Sparcs – and Rotterdam-based shipping firm Workships, for marine operations and as equal joint-venture shareholder.
Close up - BMO's offshore wind measurement technology
Wind industry technology start-up BMO Offshore, together with three Dutch partners, has entered the offshore wind market with a mobile “floating-to-fixed” service innovation that it says will cut wind costs by half over one year. This will be achieved thanks to a number of savings, including removing the need for €200,000-250,000/day jack-up vessels and for the installation permits existing technology currently requires.
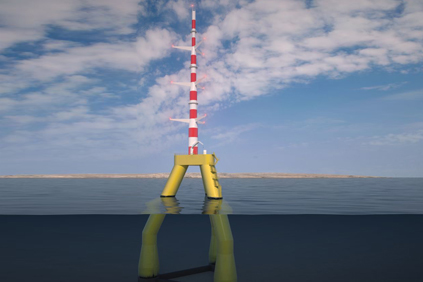